An unexpected way to upcycle: Plastic waste transforms into soap
Guoliang 'Greg' Liu of the Department of Chemistry has discovered a new method of recycling plastics — from milk cartons, food containers, and plastic bags — into soap. The method: Heat the long carbon chains in the plastics then quickly cool them.
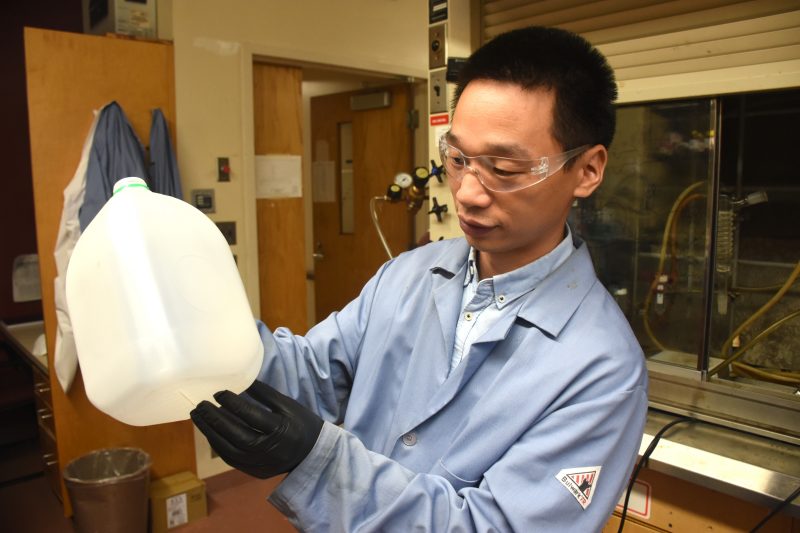
A team led by Virginia Tech researchers has developed a new method for upcycling plastics into high-value chemicals known as surfactants, which are used to create soap, detergent, and more.
Plastics and soaps tend to have little in common when it comes to texture, appearance, and, most importantly, how they are used. But there is a surprising connection between the two on a molecular level: The chemical structure of polyethylene — one of the most commonly used plastics in the world today — is strikingly similar to that of a fatty acid, which is used as a chemical precursor to soap. Both materials are made of long carbon chains, but fatty acids have an extra group of atoms at the end of the chain.
Guoliang “Greg” Liu, associate professor of chemistry in the Virginia Tech College of Science, had long felt this similarity implied that it should be possible to convert polyethylene into fatty acids — and with a few additional steps to the process — to produce soap. The challenge was how to break a long polyethylene chain into many short — but not too short — chains and how to do it efficiently. Liu believed there was the potential for a new upcycling method that could take low-value plastic waste and turn it into a high-value, useful commodity.
Having considered the question for some time, Liu was struck by inspiration while enjoying a winter evening by a fireplace. He watched the smoke rise from the fire and thought about how the smoke was made up of tiny particles produced during the wood’s combustion. Although plastics should never be burned in a fireplace for safety and environment reasons, Liu began to wonder what would happen if polyethylene could be burned in a safe laboratory setting. Would the incomplete combustion of polyethylene produce “smoke” just like burning wood does? If someone were to capture that smoke, what would it be made of?
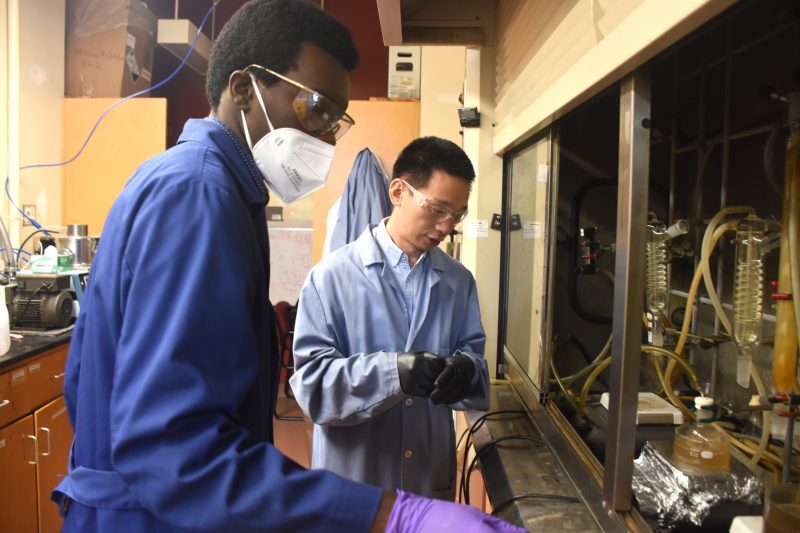
“Firewood is mostly made of polymers such as cellulose. The combustion of firewood breaks these polymers into short chains, and then into small gaseous molecules before full oxidation to carbon dioxide,” said Liu, holder of the Blackwood Junior Faculty Fellowship of Life Sciences in the Department of Chemistry. “If we similarly break down the synthetic polyethylene molecules but stop the process before they break all the way down to small gaseous molecules, then we should obtain short-chain, polyethylene-like molecules.”
With the help of Zhen Xu and Eric Munyaneza, two Ph.D. chemistry students in Liu’s lab, Liu built a small, oven-like reactor where they could heat polyethylene in a process called temperature-gradient thermolysis. At the bottom, the oven is at a high enough temperature to break the polymer chains, and at the top, the oven is cooled to a low enough temperature to stop any further breakdown. After the thermolysis, they gathered the residue — similar to cleaning soot from a chimney — and found that Liu’s hunch had been right: It was composed of “short-chain polyethylene,” or more precisely, waxes.
This was the first step in developing a method for upcycling plastics into soap, Liu said. Upon adding a few more steps, including saponification, the team made the world’s first soap out of plastics. To continue the process, the team enlisted the help of experts in computational modeling, economic analysis, and more.
Some of these experts were introduced to the team through connections with the Macromolecules Innovation Institute at Virginia Tech. Together, the group documented and refined the upcycling process until it was ready to be shared with the scientific community. The work was published today in the popular journal Science.
“Our research demonstrates a new route for plastic upcycling without using novel catalysts or complex procedures. In this work, we have shown the potential of a tandem strategy for plastic recycling,” said Xu, lead author on the paper. “This will enlighten people to develop more creative designs of upcycling procedures in the future.”
Although polyethylene was the plastic that inspired this project, the upcycling method can also work on another type of plastic known as polypropylene. These two materials make up much of the plastic consumers encounter every daily, from product packaging to food containers to fabrics. One of the exciting features of Liu’s new upcycling method is that it can be used on both these plastics at once, meaning that it’s not necessary to separate the two from each other. This is a major advantage over some recycling methods used today, which require careful sorting of plastics to avoid contamination. That sorting process can be quite difficult, because of how similar the two plastics are to each other.
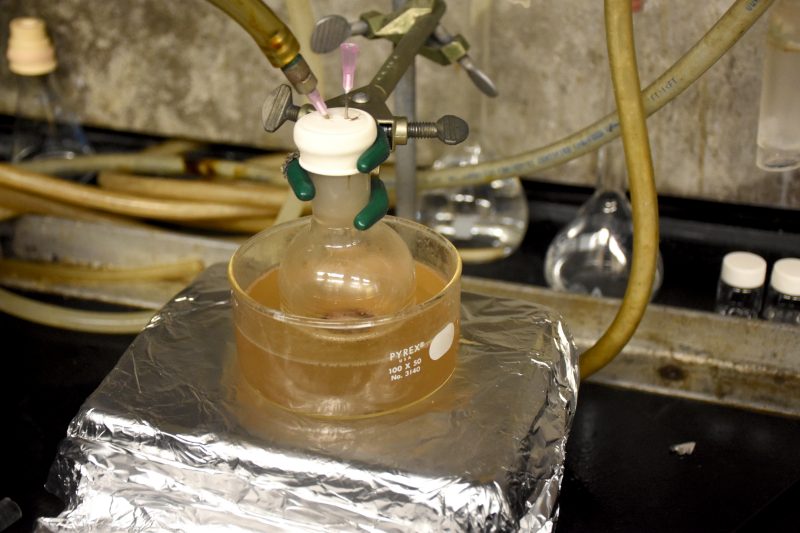
Another benefit of the upcycling technique is that it has very simple requirements: plastic and heat. Although the later steps in the process require some additional ingredients to convert the wax molecules into fatty acids and soap, the initial transformation of the plastic is a straightforward reaction. This contributes to the method’s cost-effectiveness as well as its comparatively small environmental impact.
For upcycling to be effective on a large scale, the final product must be valuable enough to cover the costs of the process and make it more economically attractive than alternative recycling options.
Although soaps may not initially seem like a particularly expensive commodity, they can actually be worth double or triple the price of plastics when compared by weight. Currently, the average price of soap and detergent amounts to about $3,550 per metric ton, and that of polyethylene is about $1,150 per metric ton. Furthermore, the demand for soaps and related products is comparable to the demand for plastics.
This research lays the groundwork for a new way to reduce waste by channeling used plastics into the production of other useful materials, Liu said. Over time, he hopes recycling facilities around the world will begin to implement this technique. If so, then consumers can expect to one day have the opportunity to buy revolutionary sustainable soap products that also lead to reduced plastic waste in landfills.
For this reason, turning plastics into soaps can be demonstrated to be economically viable, added Liu, who is also an affiliated faculty member of the nanoscience program, part of the College of Science’s Academy of Integrated Science as well as the Department of Materials Science and Engineering in the Virginia Tech College of Engineering.
“It should be realized that plastic pollution is a global challenge rather than a problem of a few mainstream countries. Compared to a sophisticated process and complex catalyst or reagent, a simple process may be more accessible to many other countries worldwide,” Xu said. “I hope this can be a good start for the war fighting plastic pollution.”
Researchers from the Department of Chemical Engineering also were part of this project and the resulting research paper.